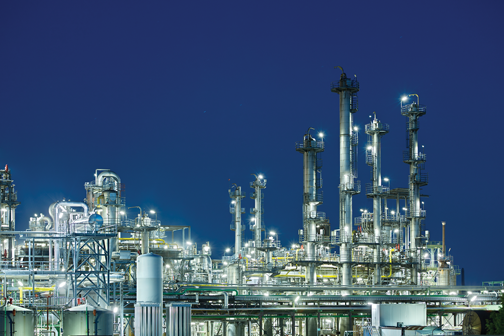
Critical Importance of Air Quality
Control rooms are utilized by large-scale refineries to monitor and control plant operations. The control room and network of control equipment are essential to plant operation and enable these facilities to maintain the highest efficiency possible. If the control room malfunctions, it can cost a plant tens of thousands of dollars per hour.
Particulate and corrosive gaseous contaminants have become a serious problem for these control rooms, sometimes resulting in catastrophic failures of equipment. These contaminants enter the control rooms in a variety of ways, including outdoor ventilation systems, adjacent interior areas, and with individuals entering and exiting the room.
Types of Failures
Failures due to particulate and contaminant dust are generally classified as:
- Mechanical effects, including obstruction of cooling airflow, interference of moving or optical parts, and deformation of surfaces
- Chemical effects, including corrosion of electrical components, due to dust comprised of sulfur and chlorine bearing salts
- Electrical effects, including impedance changes and electronic circuit conductor bridging
Corrosive Contaminant Risk
Sulfur-bearing gases, such as sulfur dioxide (SO2) and hydrogen sulfide (H2S), are the most common gases causing corrosion of electronic equipment. Once introduced into a control room, these gaseous contaminants lead to deterioration of copper surfaces and silver solder used on computer circuit boards, leading to intermittent and hard failures. These forms of corrosion can cause failure by impeding the flow of electricity. Elimination of corrosive contaminants is therefore essential in maintaining data center equipment reliability.In response to these problems, ISA (Instrumentation, Systems, and Automation Society) developed a standard to classify control rooms and process control environments – ISA 71.04. Most equipment manufacturers require that the control room environment meet the ISA G1 - Mild classification to maintain a reliable communication network in industrial environments.
Optimize Your Environment
Protection of an industrial control room includes at a minimum pressurization with purified air. This prevents corrosive gases from infiltrating the control room and causing corrosion problems. Additionally, recirculation air may require cleaning if the room is a high traffic area or there are other internal sources of contaminants.Supplemental real-time monitoring, such as AAF’s SAAFShield Technology, is recommended to enable quick reaction to outdoor events that may introduce corrosive gases into control rooms. Real-time monitoring is also recommended in control rooms with gas-phase filtration air cleaning systems, in order to track the efficiency of the filters.